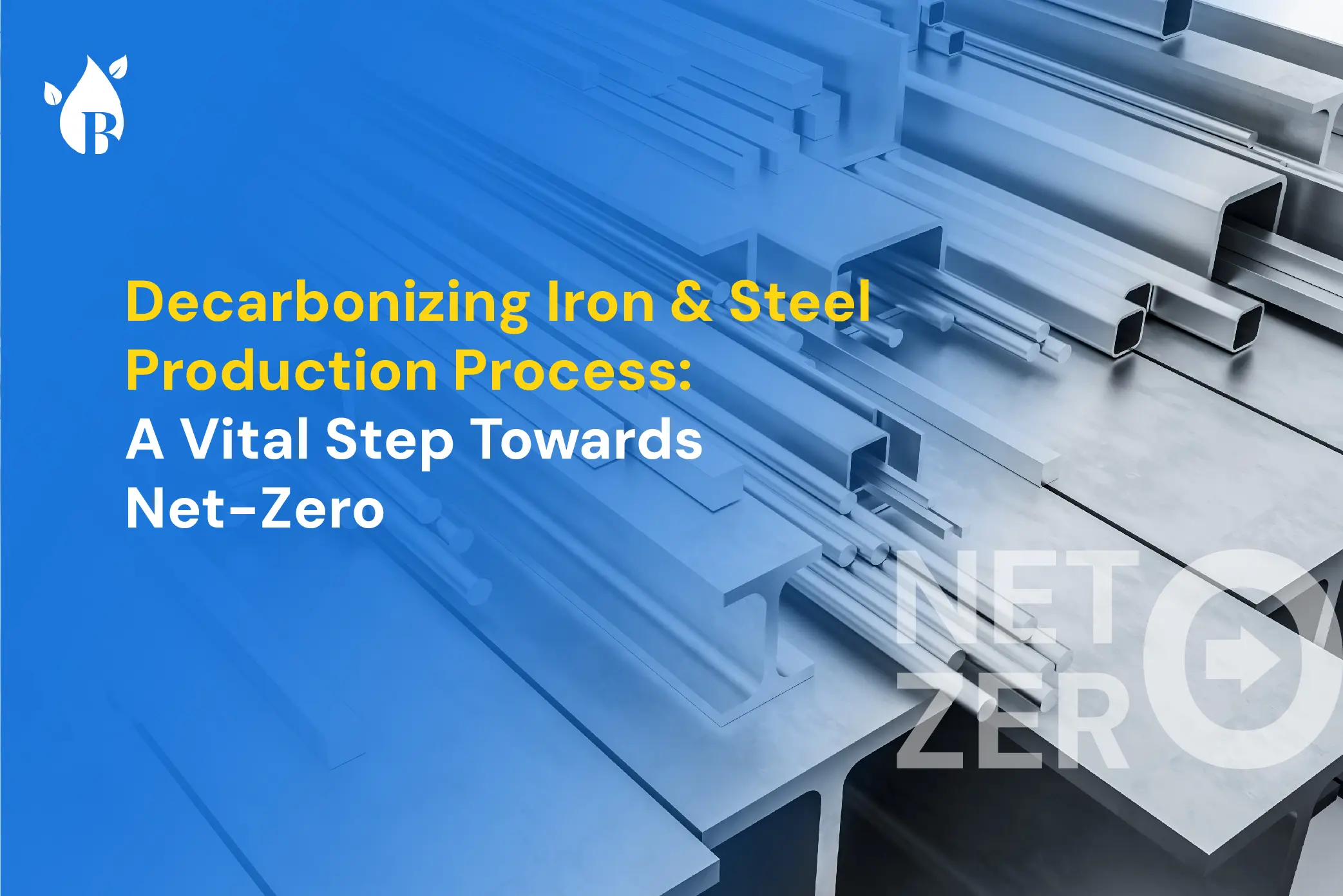
Explore the crucial journey of decarbonizing the iron and steel industry, a vital step in achieving a net-zero future. Learn more about existing production processes and sustainable innovations that shape a greener, more environmentally responsible steel production process.
Steel is an integral component of modern society and is relied upon daily for its wide range of applications such as building houses, bridges, and manufacturing cars and trucks. Also, renewable energy technologies (wind turbines, solar panels, electric vehicles, dams etc) are reliant on steel for their construction. This versatility shows that this sector holds an indispensable value. In this blog, we’ll look at why it is important to decarbonize the iron and steel sector and look into how.
Why is it Important to Decarbonize Iron and Steel?
Since 1970, the demand for steel has witnessed a substantial surge due to global economic growth, urbanization, and industrialization. As these trends persist, the consumption of steel is projected to rise in parallel. Consequently, the total CO2 emissions stemming from the iron and steel sector have also experienced a notable increase over the past few decades.
Presently, the steelmaking process alone accounts for over 3 billion MT of CO2 emissions annually, making it the industrial sector with the most significant impact on climate change. In fact, steel production contributed a staggering 7-9% of all human-made greenhouse gas emissions in the previous year, as reported by the World Steel Association.
Direct CO2 intensity of the iron and steel sector in the Net Zero Scenario, 2010-2030
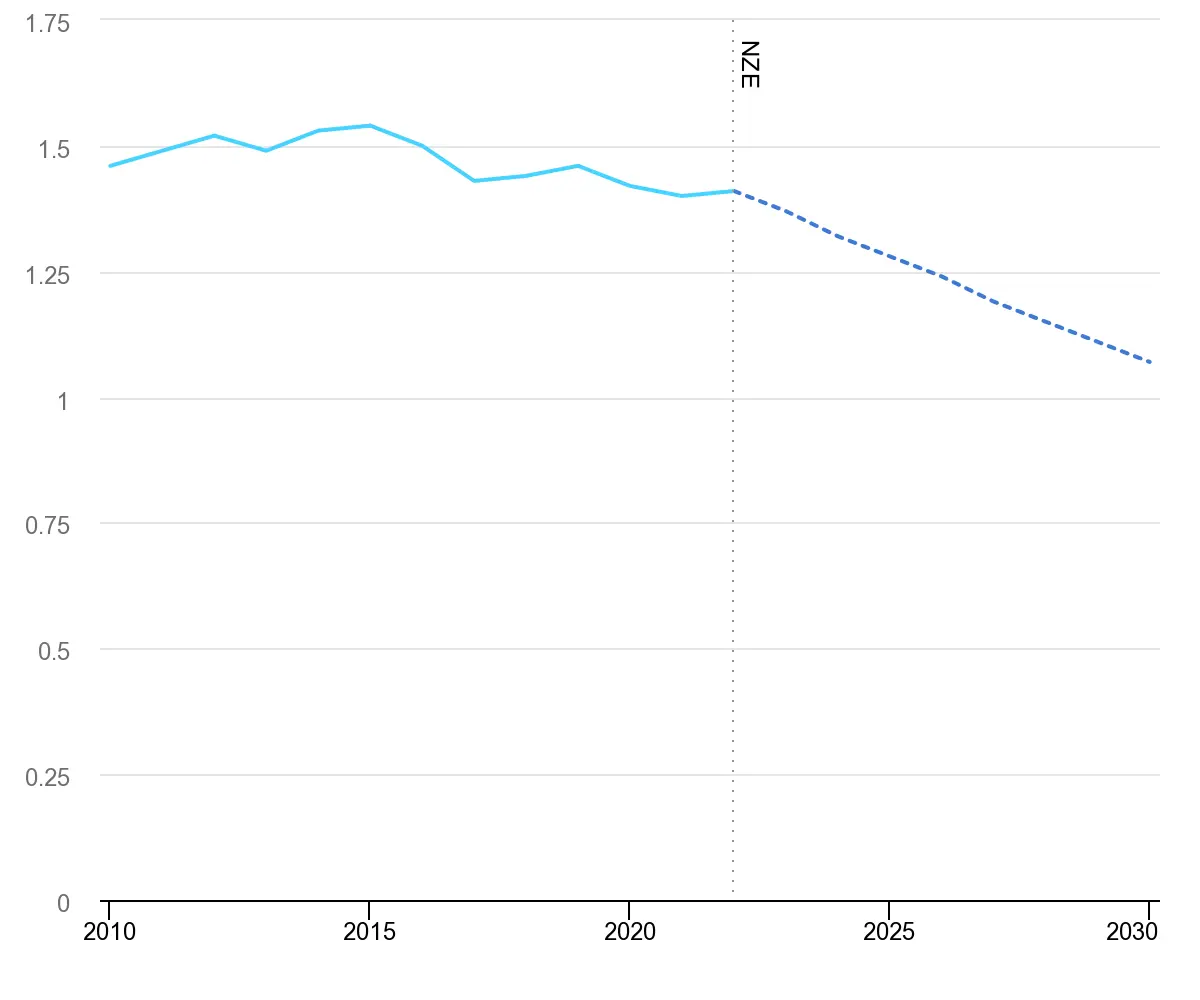
With global steel demand expected to reach 2.5 billion metric tons per year by 2050, this environmental burden is set to grow further. However, an analysis of the necessary reduction in global carbon emissions to limit global warming to a maximum of 2°C above pre-industrial levels, in line with the goals of the 2015 Paris climate agreement, suggests that the steel industry must reduce its annual emissions to approximately 500 million metric tons of CO2 by 2050. Achieving this target necessitates a revolutionary change in steelmaking technology, backed by substantial investments amounting to hundreds of billions of dollars.
Looking at the larger picture, the urgency to achieve net-zero CO2 emissions has driven both the industry and governments to dedicate significant efforts to develop the essential technologies, policies, and organizations required for decarbonizing the sector.
Iron and Steel Production Process
The process of steelmaking is highly energy-intensive and results in significant emissions due to the need for high temperatures and a carbon source to drive reactions.
There are two main routes for steel production:
The key distinction between these routes lies in the raw materials they utilize. The BF-BOF route mainly relies on iron ore, coal, and recycled steel, while the EAF route predominantly uses recycled steel and electricity. Depending on the plant setup and availability of recycled steel, other sources of metallic iron like direct-reduced iron (DRI) or hot metal may also be employed in the EAF route.
The key distinction between these routes lies in the raw materials they utilize. The BF-BOF route mainly relies on iron ore, coal, and recycled steel, while the EAF route predominantly uses recycled steel and electricity. Depending on the plant setup and availability of recycled steel, other sources of metallic iron like direct-reduced iron (DRI) or hot metal may also be employed in the EAF route.
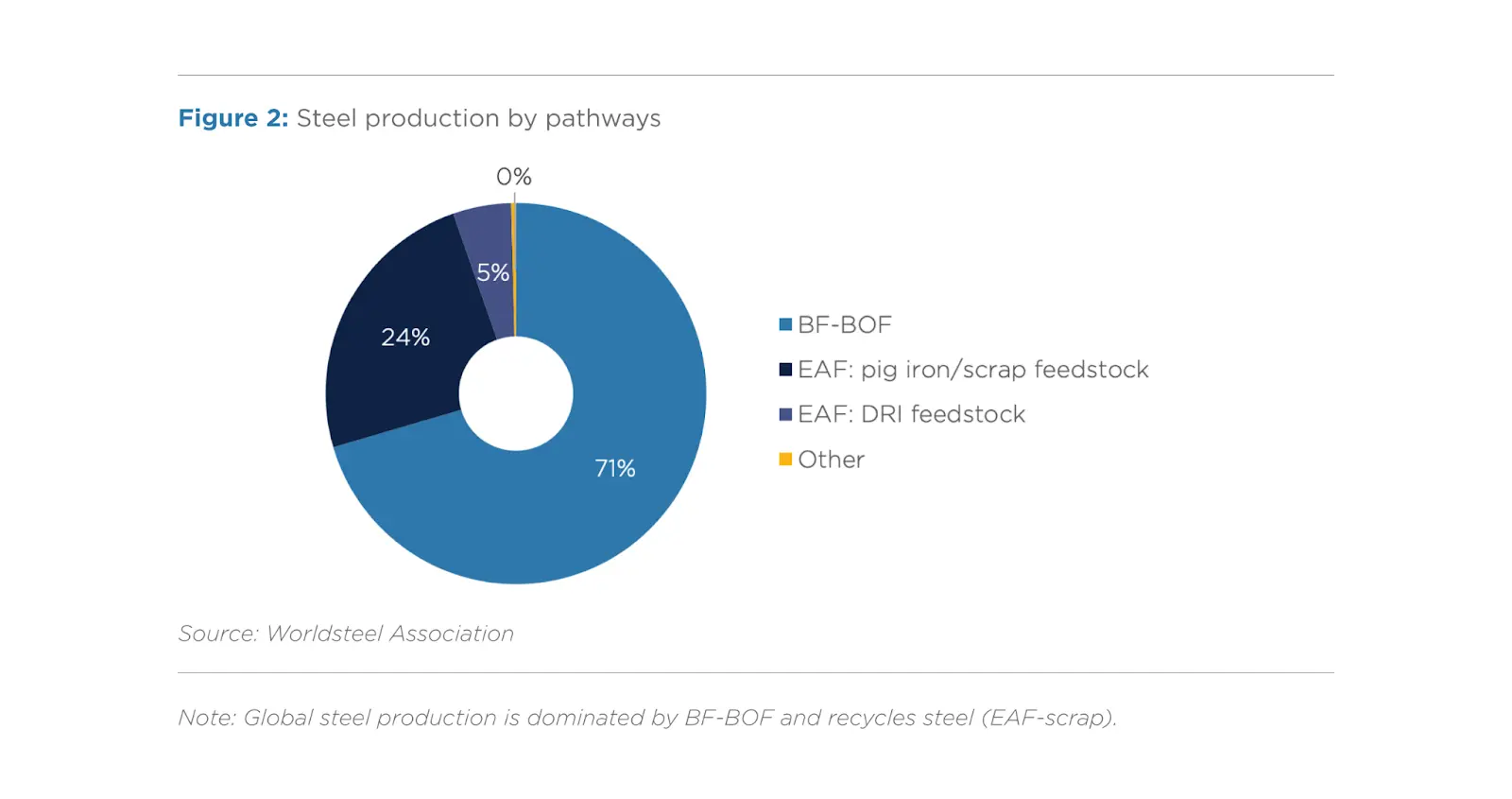
Around 70% of global steel production employs the BF-BOF route, which involves reducing iron ores to iron, also known as hot metal or pig iron. The iron is then transformed into steel in the BOF. The steel is cast and rolled before being delivered in various forms like coil, plate, sections, or bars.
In contrast, electric arc furnaces (EAF) utilize recycled steel melted by electricity to produce steel. The desired chemical composition is achieved by introducing additives such as alloys, with the option of oxygen injection supplemented by electrical energy. The downstream process stages of casting, reheating, and rolling are similar to those found in the BF-BOF route. About 30% of steel production is via the EAF route.
A third alternative, the open hearth furnace (OHF), which accounts for approximately 0.4% of global steel production, is energy-intensive and declining in popularity due to its environmental and economic drawbacks.
“An analysis suggests that the steel industry must reduce its annual emissions to approximately 500 million metric tons of CO2 by 2050 to limit global warming to a maximum of 2°C above pre-industrial levels, in line with the goals of the 2015 Paris climate agreement.”
How Do We Decarbonize Iron and Steel Manufacturing?
In the conventional production of steel, fossil fuels are burned in traditional steel furnaces to generate the high temperatures required for smelting raw iron and carbon into steel. During this process, carbon is used to extract oxygen from iron ore, turning it into pig iron, a fundamental material in the steel industry. This method results in the emission of harmful greenhouse gases.
An eco-friendly alternative to this approach involves the use of Electric Arc Furnaces (EAFs). EAFs have the advantage of being able to recycle steel scrap, significantly reducing the process emissions associated with creating new steel from iron ore. Moreover, EAFs can be powered by renewable sources of electricity, eliminating energy-related emissions.
Despite these advancements, steel production remains energy-intensive and continues to contribute significantly to greenhouse gas emissions. To combat these challenges, various decarbonization pathways are being explored through a dedicated program. These pathways include:
1. Exploring Alternative Iron and Steelmaking Processes: Researchers are investigating innovative methods to produce steel that are less reliant on traditional carbon-intensive processes.
2. Hydrogen Injection into Blast Furnaces: Introducing green hydrogen into blast furnaces could potentially reduce emissions, as hydrogen can replace carbon as a reducing agent, leading to cleaner steel production.
3. Utilizing Clean Electricity Sources: Increasing the use of clean electricity sources and alternative fuels like biofuels, to power steelmaking processes can significantly reduce emissions.
4. Promoting the Use of Scrap: Encouraging the use of recycled steel scrap in manufacturing processes can minimize the need for new raw materials, thereby decreasing emissions associated with the extraction and processing of iron ore.
5. Integrating Hydrogen into Existing Processes: Besides injection into blast furnaces, finding other ways to incorporate hydrogen into existing steelmaking processes can lead to more environmentally friendly production methods.
To support these efforts, ongoing technology development focuses on creating a robust infrastructure capable of supplying green hydrogen and renewable electricity production methods. This infrastructure is essential for enabling the steel industry to transition towards greener practices and significantly reduce its carbon footprint. Through these innovative approaches and technological advancements, the industry aims to revolutionize steel production, making it more sustainable and environmentally friendly.